What service do we provide?

Global Maintenance
As the specialist in freezers and chillers, we operate with an integrated service network around the world for servicing and maintenance of our own equipment as well as spiral freezers from other manufacturers.
Flexible design
​
A vertical plate freezer consists of a number of plates, mounted vertically, through which a refrigerant runs. The product is simply poured into the pockets between the plates and will be frozen as blocks.
​

Preventive maintenance
Preventative maintenance is crucial for ensuring the uninterrupted operation of your industrial refrigeration and freezing systems. Regular maintenance helps to prevent unexpected breakdowns, which can be significantly more costly and disruptive than scheduled upkeep. By investing in preventative maintenance, you minimize the risk of production halts that can lead to expensive downtime and lost revenue. Regular servicing not only extends the lifespan of your equipment but also enhances its operational efficiency, ensuring it runs at peak performance.
​
Routine checks and servicing allow for the early detection of potential issues, preventing them from escalating into major problems that require costly repairs or replacements. Additionally, well-maintained systems are more energy-efficient, leading to lower utility bills and a reduced environmental impact. Preventative maintenance also ensures compliance with safety and regulatory standards, safeguarding your workforce and avoiding legal complications. Ultimately, a proactive approach to maintenance secures your investment, improves reliability, and promotes a smooth and efficient production process.
Optimizing and retrofitting
At Advanced Freezers, we specialize in optimizing and retrofitting industrial refrigeration and freezing installations. Our expertise is not limited to just improving individual units but extends to comprehensive line optimization. We analyze your entire production process to identify inefficiencies and implement solutions that enhance overall performance. Our team of skilled engineers can perform major modifications to your systems, such as increasing the number of tiers in your freezer or converting low-tension systems to direct drive for improved reliability and performance.
​
Our optimization services aim to maximize throughput, reduce energy consumption, and minimize waste. Whether it involves upgrading components to the latest technology, reconfiguring layouts for better workflow, or integrating advanced control systems, we tailor our solutions to meet your specific needs. Retrofitting existing installations with state-of-the-art technology not only boosts performance but also extends the operational life of your equipment, providing a cost-effective alternative to complete system replacement. Our goal is to deliver customized, high-impact improvements that drive your business forward.
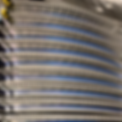

Recommending spare parts
Having essential spare parts on hand is critical to maintaining continuous production and avoiding costly downtime. In the event of a breakdown, being able to quickly replace components such as motors or conveyor belts can drastically reduce downtime, keeping your operations running smoothly. Extended production stoppages can lead to significant financial losses, affecting your bottom line and customer satisfaction.
​
With over 30+ years of experience in the industry, we have the expertise to provide accurate and valuable recommendations on which spare parts you should keep in stock. Our deep understanding of industrial refrigeration and freezing systems allows us to advise you on the most critical components to have readily available. We can help you develop a strategic spare parts inventory that ensures you are prepared for any eventuality, minimizing production interruptions and associated costs. Trust us to provide you with the insights and support needed to maintain a seamless production process, ensuring your operations remain efficient and reliable.
24/7 support service
Our 24/7 support service is a cornerstone of our commitment to our customers. We understand that issues can arise at any time, and immediate assistance is crucial to minimizing disruption. Our dedicated support team is always available to assist you, providing prompt responses to any emergency. Whether it’s a minor issue or a major breakdown, we ensure that our skilled technicians are ready to dispatch to your site whenever you need them, day or night.
Our comprehensive support service goes beyond emergency responses. We offer continuous monitoring and remote diagnostics to detect and address potential issues before they escalate.
Our customer service team is always reachable, ensuring you receive the guidance and support needed to keep your operations running smoothly. We pride ourselves on our reliability and dedication, building strong, long-lasting relationships with our clients. At Advanced Freezers, we are known for our unwavering support, ensuring that you are never left stranded and that your production remains uninterrupted. Trust us to be there for you, 24/7, providing the highest level of service and support.
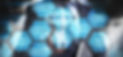